What is Porosity in Welding: Ideal Practices for Staying Clear Of Porous Welds
What is Porosity in Welding: Ideal Practices for Staying Clear Of Porous Welds
Blog Article
Porosity in Welding: Identifying Common Issues and Implementing Best Practices for Avoidance
Porosity in welding is a pervasive problem that frequently goes undetected until it creates considerable troubles with the integrity of welds. In this conversation, we will certainly check out the vital elements adding to porosity development, examine its damaging effects on weld efficiency, and discuss the finest techniques that can be adopted to lessen porosity occurrence in welding processes.
Typical Sources Of Porosity

Another regular culprit behind porosity is the visibility of impurities externally of the base metal, such as oil, grease, or corrosion. When these impurities are not effectively eliminated before welding, they can evaporate and come to be entraped in the weld, triggering flaws. Using filthy or damp filler products can present pollutants into the weld, adding to porosity issues. To mitigate these usual reasons for porosity, extensive cleansing of base metals, proper securing gas selection, and adherence to optimum welding specifications are crucial methods in attaining high-quality, porosity-free welds.
Effect of Porosity on Weld High Quality

The presence of porosity in welding can substantially endanger the structural stability and mechanical buildings of welded joints. Porosity creates spaces within the weld steel, compromising its general strength and load-bearing capability.
One of the primary repercussions of porosity is a reduction in the weld's ductility and sturdiness. Welds with high porosity levels have a tendency to show reduced influence strength and decreased ability to warp plastically prior to fracturing. This can be specifically worrying in applications where the look at here bonded parts are subjected to vibrant or cyclic loading conditions. Porosity can click for info hinder the weld's ability to effectively transmit pressures, leading to premature weld failing and possible safety and security threats in essential frameworks. What is Porosity.
Ideal Practices for Porosity Avoidance
To enhance the structural stability and top quality of welded joints, what particular procedures can be applied to minimize the occurrence of porosity during the welding process? Utilizing the proper welding technique for the particular material being bonded, such as readjusting the welding angle and weapon placement, can better stop porosity. Normal evaluation of welds and instant remediation of any type of problems determined throughout the welding procedure are crucial techniques to stop porosity and generate premium welds.
Importance of Proper Welding Techniques
Applying appropriate welding strategies is vital in guaranteeing the architectural stability and top quality of welded joints, building upon the foundation of reliable porosity prevention steps. Extreme heat can like this lead to boosted porosity due to the entrapment of gases in the weld pool. Furthermore, utilizing the appropriate welding specifications, such as voltage, current, and travel rate, is essential for attaining audio welds with marginal porosity.
Moreover, the choice of welding procedure, whether it be MIG, TIG, or stick welding, need to line up with the details needs of the project to guarantee optimum results. Appropriate cleansing and prep work of the base steel, as well as choosing the best filler product, are also necessary components of skilled welding strategies. By sticking to these ideal practices, welders can lessen the threat of porosity formation and produce top notch, structurally audio welds.
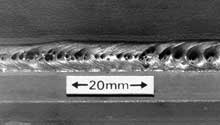
Evaluating and Quality Assurance Measures
Examining procedures are important to identify and stop porosity in welding, making sure the toughness and toughness of the last product. Non-destructive testing methods such as ultrasonic testing, radiographic screening, and aesthetic assessment are frequently utilized to identify potential problems like porosity.
Conducting pre-weld and post-weld examinations is likewise crucial in maintaining top quality control requirements. Pre-weld inspections include verifying the products, devices setups, and tidiness of the workplace to avoid contamination. Post-weld assessments, on the other hand, analyze the final weld for any flaws, including porosity, and verify that it meets defined standards. Carrying out a comprehensive high quality control plan that includes comprehensive screening procedures and assessments is paramount to minimizing porosity concerns and guaranteeing the total quality of welded joints.
Conclusion
To conclude, porosity in welding can be a typical concern that influences the quality of welds. By identifying the usual sources of porosity and carrying out finest techniques for avoidance, such as correct welding strategies and screening measures, welders can ensure premium quality and trustworthy welds. It is essential to prioritize prevention methods to minimize the occurrence of porosity and maintain the integrity of welded frameworks.
Report this page